Accidents can happen in the blink of an eye, companies must prioritize the health and security of their workforce, and this is where JSA comes into play. It’s a systematic approach that helps identify potential hazards and eliminates risks before they have a chance to impact employee well-being and safety.
From construction sites to office spaces, every work environment carries its own unique set of dangers. This is why businesses need to conduct a thorough JSA, so they can proactively mitigate these risks and also create a culture that values safety above all else. Below are some of the things that you need to know about it.
In the workplace, JSA will help assess the possibilities of injuries, fatalities, and accidents, and it’s a tool that many organizations need. Employers may identify and address the safety concerns before they can escalate into something worse. A safety JSA can add training and other precautions on the job site, so everyone will be more aware of what they are facing.
What Does It Do to the Employees?
It essentially empowers everyone to take ownership of their safety. When workers are actively involved in identifying some of the pitfalls, and avoiding them in their work procedures, they become more diligent and watchful. This increased awareness leads to better decision-making when faced with hazardous situations.
Also, implementing this can have a positive impact on overall productivity, because it shows everyone that companies try to prevent accidents and injuries that result in lost workdays or decreased efficiency due to disruptions caused by incidents. It’s going to promote a smoother workflow, and it’s going to be compliant with the requirements of the OSHA.
Steps to Conduct a JSA
Select the Job
All of the jobs should have a thorough JSA analysis, and they should require some changes when there are revisions in a workplace’s raw materials, equipment, and environment. It’s best to identify the frequency and severity of accidents in a specific work, and there should be a thorough analysis of potentially hazardous products or solutions that can cause illnesses.
For newly established jobs, there may be pitfalls that still need anticipation, so make sure to modify them as time goes by.
Break Down Everything into Simpler Steps
Steps should not be too general or too detailed. A good rule of thumb is to define safety procedures in ten steps and divide the job into two segments. An example is what employees should do when they have flat tires. The first thing that they can do is park their vehicle in a safe place, and it should be away from traffic, remove their tool kits and the spare, pry off the log bolts and hub caps, etc.
Job observers should be capable and experienced in doing all of the procedures of the job, and the observations should be done during normal situations and times. They might also conduct assessments at night to keep the workers safe.
How JSA Can Improve Workplace Safety and Productivity?
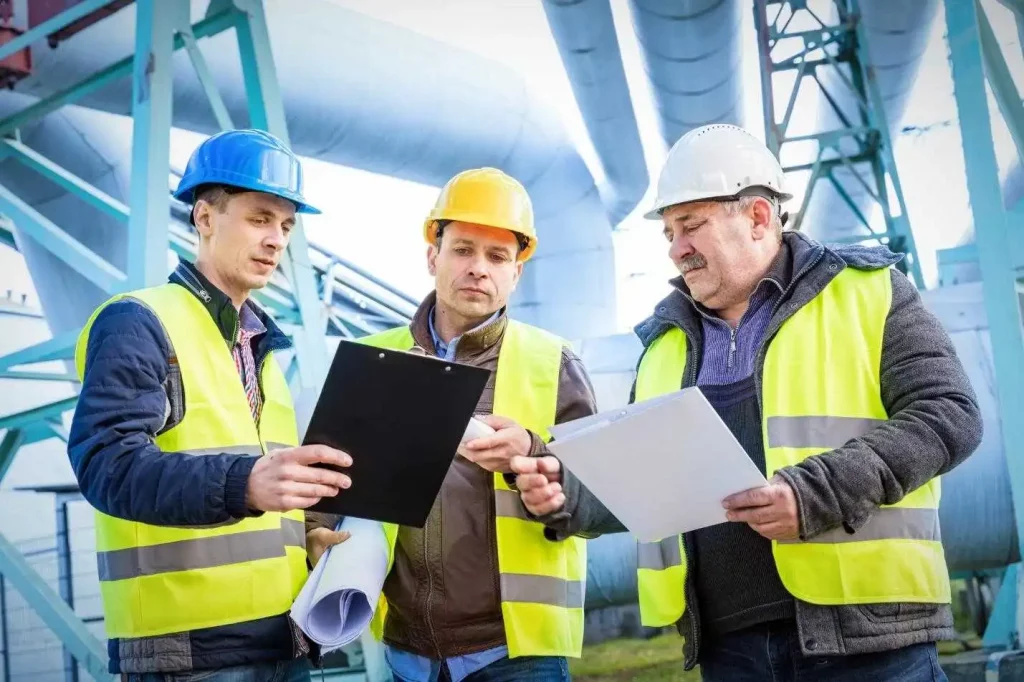
Implementing a Job Safety Analysis in your workplace can have significant benefits for both safety and productivity. When you break down job tasks, identify potential hazards, and implement preventive measures, JSA helps create a safer work environment, and you can see more about this process on this webpage.
An increased awareness of everyone involved and taking action can prevent accidents from happening in the first place. It’s also going to significantly improve the communication levels of the workers, where they can foster knowledge-sharing and collaboration when needed. It’s not only going to strengthen their relationships but also help the new ones become more used to their jobs.
Boosting productivity can also be a result of JSA, where the inefficiencies can easily be identified. A team is going to optimize the workflow and streamline the process, and they can eliminate redundant actions and wasted time. Employees can focus on essential tasks without compromising quality or efficiency.
Also, when everyone feels safe at work due to effective hazard control measures resulting from JSA implementation, they tend to be more engaged and motivated. A positive work environment contributes to higher employee satisfaction levels, which ultimately translate into increased productivity.
Wrapping Up With Tips
Before starting the process, it’s essential to have buy-in from top-level management. This ensures that resources, time, and training can be allocated appropriately. Include employees from various departments since their input is valuable as they have firsthand experience with job tasks and potential hazards. Read about hazards at this link: https://www.safeopedia.com/definition/646/workplace-hazard.
Break down each job into individual tasks or steps. This helps to analyze potential risks associated with each task more effectively. Once you’ve identified the tasks, assess the hazards and risks associated with each one. Document these findings accurately for future reference.
Determine appropriate control measures for each hazard identified during the analysis phase of JSA implementation. Share the results of your JSA with all relevant personnel within your organization, including supervisors, managers, and workers directly involved in performing the analyzed jobs.
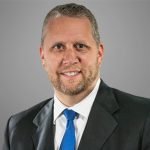
Michael C Vang is a passionate blogger. He has been blogging since 2013 on a variety of topics. He is committed to creating informative and engaging content that helps readers learn more about everything.